Explore related products
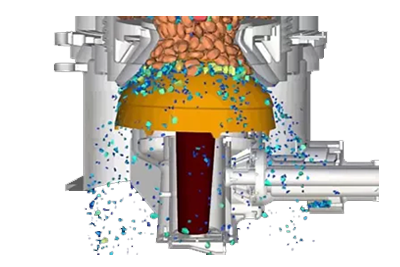
Ansys Rocky
Rocky DEM is the industry-leading discrete element method (DEM) software used for particle dynamics, simulating the motion of granular and discontinuous material.
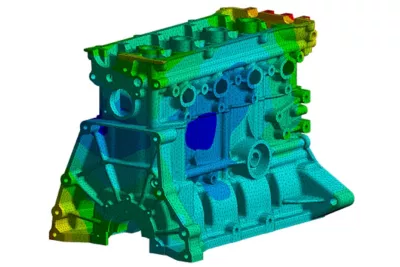
Ansys Mechanical
Structural analysis with Ansys Mechanical provides robust general purpose stress, thermal, modal and fatigue simulations for fast and accurate solutions.
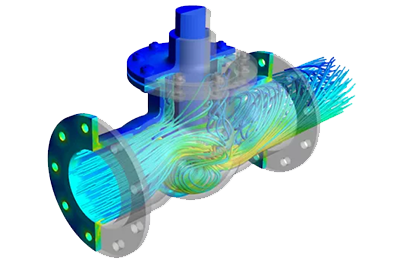
Ansys Fluent
Ansys Fluent is the industry-leading fluid simulation software known for its advanced physics modelling capabilities and industry leading accuracy.
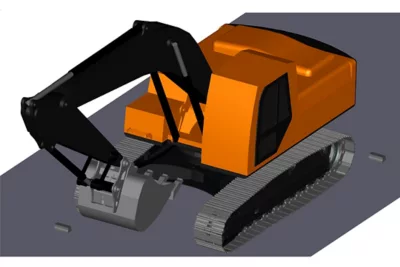
Ansys Motion
This multibody dynamic solver for analysis of rigid and flexible bodies is capable of accurate evaluation of physical events through the analysis of a whole system.

Ansys Granta
Ansys Granta is a scalable solution to create, control and store your company’s valuable material data, enabling you to capitalise on your organisation’s Material Intelligence.