Flownex for Spaceflight
Simulating modern space propulsion systems such as cryogenic liquid rocket engines involve many complexities such as highly interconnected components, different heat transfer modes and combustion processes. Flownex® is the industry leader in 1D CFD software, allowing for the integrated simulation of large interconnected thermal fluid systems.
Overview
From rapid rocket engine cycle designs to detailed component development: Flownex® has the capability to model and simulate large interconnected rocket engine systems. Using Flownex®, pre-burners with complex combustion reactions can be simulated, flow control strategies can be investigated, turbopumps with real-time power matching can be implemented and much more.
Liquid-fuelled Rocket engines have come a long way since the first-ever rocket launch by Robert Goddard on March 16th 1926. Today more sophisticated rockets have been developed, such as the SpaceX Raptor engine. Different liquid rocket cycles have been designed in the past few decades: improving efficiency, power, and safety. This has led to time consuming and costly physical testing and design calculations. To reduce R&D cost and development time, 1D system simulation can be incorporated into the design process.
Cycle Design Evaluation
Flownex® can be used for the rapid design and evaluation of engine cycles. Different system configurations can be compared with ease. The efficiency of the open or gas generator cycle, can be compared to the more efficient oxidizer-rich cycle which reuses the hot gasses of the pre-burner. Further investigation can be done on more intricate closed cycle designs. This includes closed, fuel rich, dual shaft cycles and full flow, staged combustion cycles.
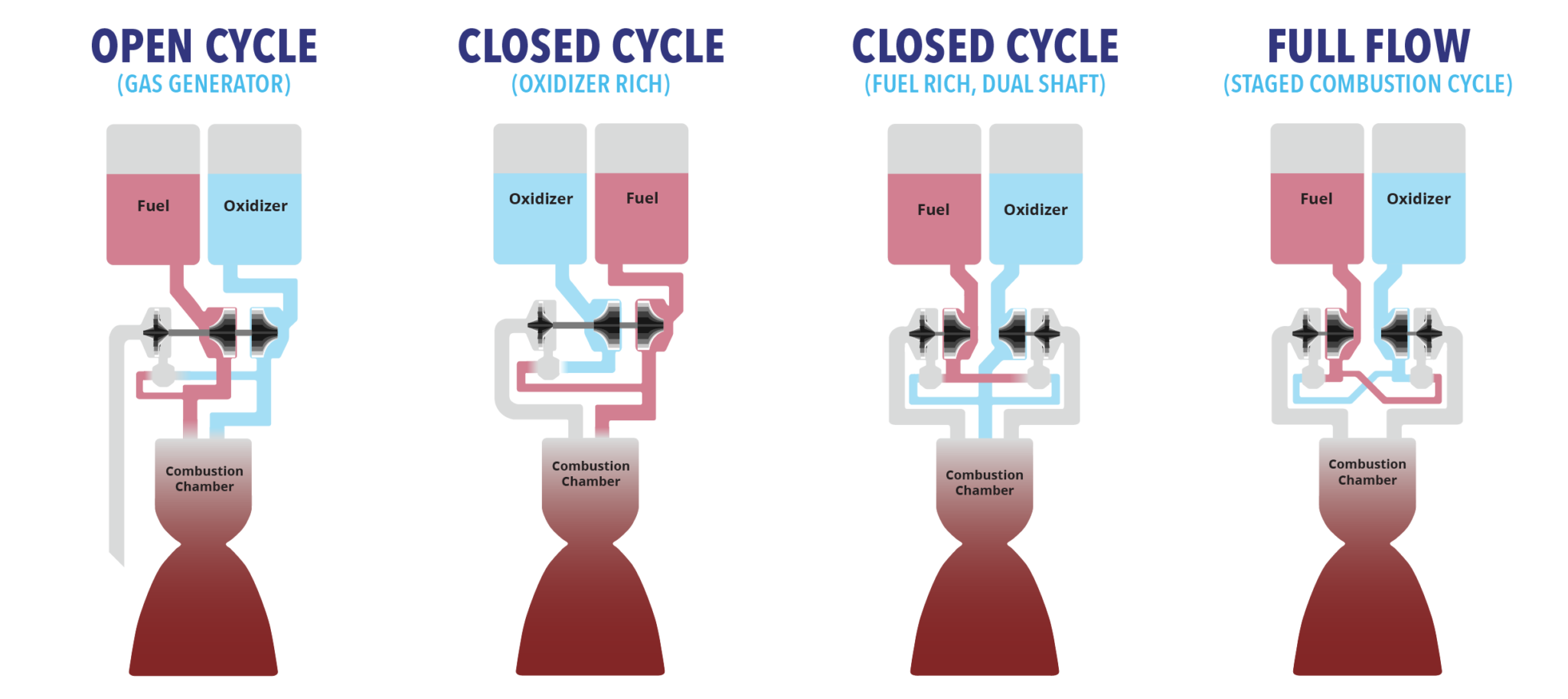
Cryogenic Rocket Fuel Modelling
Flownex® allows for the simulation of the different parts of a liquid-fuel cryogenic rocket model. Allowing for advanced cryogenic fuel property evaluation and the use of pre-existing turbomachinery components, Flownex allows for quick and easy system modelling and design.
PREBURNERS AND CONTROL VALVES
Flownex® allows for the modelling and design of pre burners and allows for the implementation of control systems to replicate real-life control strategies. Complex combustion reactions can be modelling, calculating off-gas products and temperatures. Multiple-branch flow property calculations can be implemented in real-time transient simulations.
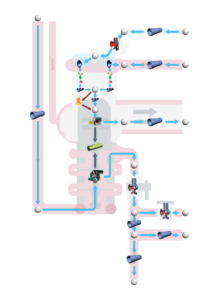
TURBOPUMPS AND FUEL LINES
Complex turbopumps can be modelled and simulated in steady-state and transient. Advanced power matching is applied which allows for calculating shaft speeds. Turbine maps and pump charts can be implemented to realise true system responses. Custom fluids for cryogenic temperature regions can be imported using NIST which allows for accurate properties evaluations.
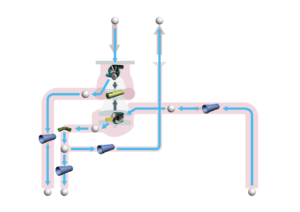
BRANCHED FLOW AND HEAT EXCHANGERS
Flownex gives you the ability to simulate flow in multiple branched sections with the inclusion of control. Several turbines and pump components can be added to one shaft allowing for complex power matching. Different methods of heat transfer can be incorporated in the system model, such as heat transfer between pipes, from ambient conditions and from combustion processes. Pressure drop components can be added such as bends, T-junctions, reducers, orifices, etc.
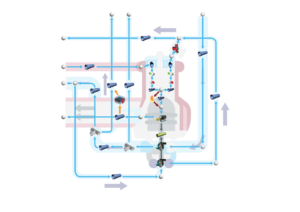
COMBUSTION CHAMBER AND THRUST NOZZLE
Flownex allows for the modelling of combustion chambers in liquid fuelled rocket engines. Combustion chamber mixing can be done together with the combustion process modelling. Phase changes can be realised, and heat rejected from combustion can be simulated. Flownex can be used to calculate the nozzle thrust giving the user the ability to simulate the resulting driving forces of a rocket.
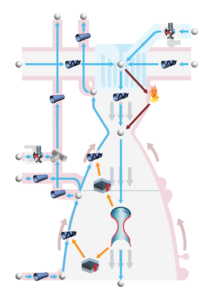
Full Integrated System Modelling and Ansys Co-Simulation
Large interdependent systems can be modelled using Flownex®. This allows for overall system response and the ability to evaluate system effects due to changing parameters. Overall efficiencies can be calculated and testing of different system configurations and concepts can be considered.
Flownex® also allows for direct coupling with Ansys Mechanical, CFX and Fluent. Complex three-dimensional conduction and flow can be integrated with Flownex® using this capability. Coupling Flownex® with Ansys reduces solving times by integrating complex three-dimensional problems with one-dimensional flow networks.
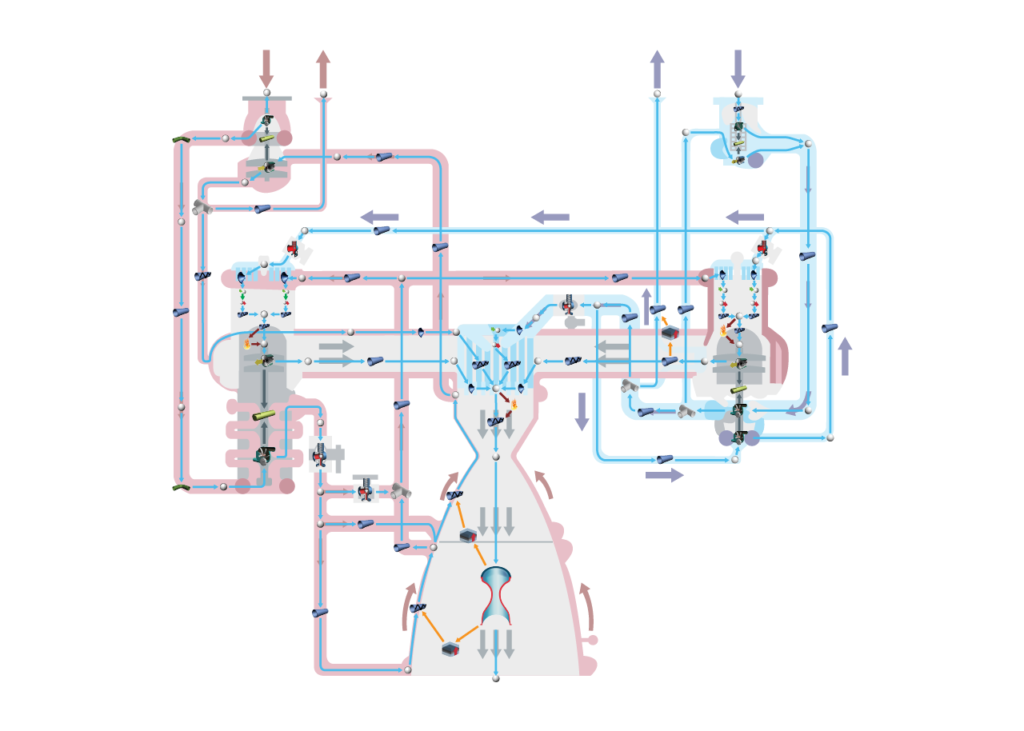
With pressure on industries to move to zero emissions, a strong focus has been put on the research and development of hydrogen applications for decarbonisation. The European Union, and others, for example, want to get to net-zero greenhouse gas emissions by 2050. One way of doing this is to implement technologies such as hydrogen fuel cells to generate electricity. Green Hydrogen, where renewable energy is used to generate hydrogen from water using a process called electrolysis, is one of the main sources of carbon-free energy currently being researched.
Want to learn more about Flownex solutions for spaceflight?
Complete the form and our team will contact you to discuss your needs.
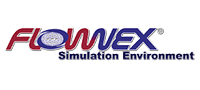