Explore related products
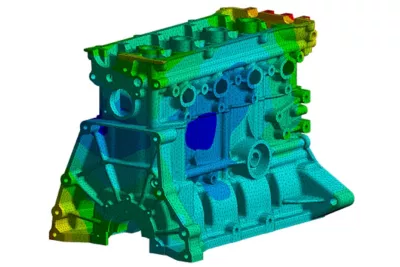
Ansys Mechanical
Structural analysis with Ansys Mechanical provides robust general purpose stress, thermal, modal and fatigue simulations for fast and accurate solutions.
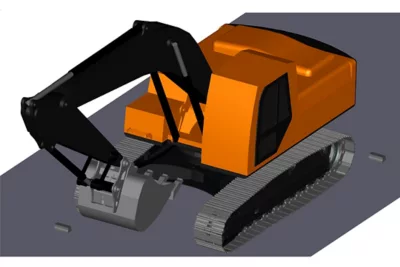
Ansys Motion
This multibody dynamic solver for analysis of rigid and flexible bodies is capable of accurate evaluation of physical events through the analysis of a whole system.

Ansys Granta
Ansys Granta is a scalable solution to create, control and store your company’s valuable material data, enabling you to capitalise on your organisation’s Material Intelligence.